(This article giving an overview of the field of Computer Aided Engineering has been written for PuneTech on our request by Dr. Ajey Walavalkar, regional manager of services and support at Ansys Fluent India, a company specializing in CAE and CFD applications and services, which has a development center in Pune. See the end of this article for more about Ajey.)
In the earlier PuneTech article “An Overview of CAD,” Yogesh and Amit have provided a very good overview of the CAD technology spectrum. There, we learnt where and how “Analysis” and “Simulations” fit in the overall scheme of CAD. This article is intended to provide a broad overview of the area called Engineering Simulations, which spans across the above mentioned “Analysis” and “Simulations” fields on the CAD canvas.
What are Engineering Simulations?
The analysis of vibrations and the dynamical behaviour due to excitation forces have been applied routinely to cable-stayed bridges using SMR devised analysis tools. Note that similar techniques have been used to analyse the resonance behaviour of large floating bridge structures.
The example shows an eigenmode of a large cable-stayed bridge (model and analysis with B2000 by The Dutch National Aerospace Research Institute (NLR)). The figure displays a vibration mode, the shape being artificially amplified to emphasize the deformation. Source http://www.smr.ch/services/csm
Let’s say you want to build a bridge. Not just any bridge, but a massive suspension bridge to rival the Golden Gate Bridge in San Francisco Bay Area. How do you decide the type of steel, the span length, the tower height, the thickness of the cables, the depth of the foundations, and other design parameters? You will wonder that if this problem was solved in the 1930s then why is it tough today? The simple answer is, ‘Solved? Yes! But at what cost and effort?’ Previously, the simple solution for most tough engineering problems was to ‘over-engineer’ the solution by building in a ‘huge factor of safety’. Today, this design process is lot more accurate and efficient. Today, the engineering team will start off by considering the effects of vehicles (weights and speeds) plying on the bridge, the wind forces that will sway the bridge, the waves that will hit the foundation, the steady long-term corrosive effects of weather, etc. These effects can studied by mathematically modeling these factors and ‘simulating’ them with a help of a computer. Such ‘simulations’ greatly help today’s engineers to come up with the exact design that is safe and that saves time and costs.
Wikipedia defines Simulation as follows:
Simulation is the imitation of some real thing, state of affairs, or process. The act of simulating something generally entails representing certain key characteristics or behaviors of a selected physical or abstract system.
Engineering simulations are simulations applied to engineering problems. These can range from simple “back of the envelope” calculations to full fledged systems simulations using High Performance Computing.
Mathematical modeling and physical modeling are two main aspects of engineering simulations. Mathematical modeling refers to the description of a particular phenomenon in terms of mathematical equations. E.g. If you wish to find out the distance a canon ball will travel when fired from a canon at certain angle, at a certain speed; you can write some mathematical expressions and solve them to calculate this distance. This is mathematical modeling. Now suppose you are firing that canon ball at a mountain cliff and the ball is going to bounce off and roll down the slopes of the mountain, how do you find out where that ball will end up? Here you need to also consider the physical structures and that leads you to physical modeling.
Uses of Engineering Simulations
Today, computer aided engineering simulations are used extensively in designing and development of almost all industrial products. In addition to product designing, simulations find their uses in troubleshooting of existing systems and research & development of new processes. Many times the field of computer aided engineering simulations is also termed as Computer Aided Engineering (CAE). There are numerous software products available in the market and they offer variety of engineering simulation capabilities. Many organizations also use their in-house built simulation software products that capture their time proven design practices.
There are many objectives in performing engineering simulations:
- During product design cycle, engineering simulations enable the designers to evaluate various design options without getting into costly prototyping and testing. Use of simulations in the design process can help narrow the design choices to very small set that can be taken to the prototyping and testing phases. Even with physical testing, one can inspect and measure only a small number of variables at few select locations. Whereas simulations can provide visual information on all the variables of interest at all locations inside the simulated space.
- Simulations can help troubleshoot deviation of actual performance of system/product from the desired one.
- Simulations can help designers and analysts to evaluate response from the product or system, to ‘highly-off’ design conditions, e.g. evaluating the safety of a nuclear reactor facility in hurricane conditions etc.
What is involved in performing engineering simulations?
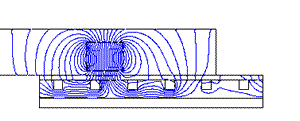
Animation of Electromagnetic Simulation showing development of magnetic flux lines. Source http://www.ansys.com/solutions/electromagnetics.asp
The domain of engineering simulations is mainly divided based on the physics that is captured in the simulation. Based on this criterion, the domain is broadly categorized as follows
- Structural analysis Simulations
- Thermal & Fluids Simulations or Computational Fluid Dynamics (CFD) simulations
- Electronic Design Automation
In any type of engineering simulation, there are three main stages.
- Pre-processing: This involves determining the region in space that one will need to use in simulation. This region, (with all the necessary geometry details that are needed to attain the goals of the simulation) is then drafted on a computer using various CAD software tools. This space domain is then discretized into various small volumes or elements called computational cells. This is called meshing or gridding of the domain. Depending on the physics involved, the extent of the physical domain, the accuracy desired and the computational resources that are available, this mesh or grid can range from a few hundred cells to few hundred million cells. Ansys recently broke the Billion cell barrier.
- Solving the governing equations: This step involves solving the governing mathematical equations that describe the physics that one desires to capture at all the computational cells. Finite Element Method (FEM), Finite Volume Method (FVM) and Finite Difference Method (FDM) are the most commonly used numerical techniques that enable solving the governing partial differential equations on discretized domain on computers. To perform these calculations, many inputs need to be provided. The results achieved from the simulations are directly dependent on the inputs provided. Techniques of parallel computing enable use of multiple cpus on a network to be used for solving a single simulation. In this technique, if you have a mesh with say 2 million cells, and have a network cluster of 8 cpus, each CPU can solve equations for 0.25 million cells and thus the simulation time can be reduced significantly as compared to a single CPU solving equations for all 2 million cells.
- Post-processing: This stage involves understanding and analyzing the results of the simulations. The simulation software tools provide a mix of visual as well as alpha-numeric reporting of various variable of interest to the user so that the user can derive the information from the simulation needed to fulfill their objectives.
Most of the engineering simulation software tools provide connectivity to variety of CAD drafting packages so that geometries can be imported in from various different sources. Many of them provide ability to customize the solvers such that users can add their own/ proprietary physics/knowledge in the simulations. The post-processing allows results to be ported to various other analysis tools including optimization tools. Through these customizations, many users of these software tools have embedded the engineering simulation technology deep into their design process. Of the software tools available in the market, many are general tools that can be used by any industry vertical where as there are few tools that are developed for only one or few industry verticals and are easier to use to simulate applications in that particular industry.
Future of engineering simulations
Animation of FLUENT CFD simulation of flow over an elite male swimmer in the glide position. Source: http://www.fluent.com/news/pr/pr69.htm.
At present, most of the software tools available in the market are solving various physics involved in the real life process or equipment separately. However, in reality all these physics occur simultaneously and affect one another. The world of engineering simulations is moving rapidly towards incorporating multiple physics and their interactions to provide more reliable predictions. The engineering product development community is exploring, what is known as “Simulation Driven Product Development”, so that full benefits of engineering simulation technology can be leveraged to their competitive advantage. Some of the major software providers in this space have already started offering multi-physics solvers that enable organizations to march in this direction.
Another new facet that is coming in focus now is of knowledge management. Use of these simulation software tools, is generating a lot of engineering knowledge which the companies would like to leverage in their future design processes. With this need in mind, integrated engineering knowledge management platforms that will work seamlessly with the engineering simulation tools are being developed.
Engineering Simulations scene in Pune
Pune has attracted most of the main players in this exciting domain.
Ansys Inc, one of the leading companies in developing the engineering simulation software tools is present in Pune. Ansys has development, testing, sales, support and services functions for India based as well as worldwide customers being conducted out of the Pune office. Ansys develops structural analysis, CFD, EAD as well as optimization tools that are used widely in almost all industry segments.
In addition to Ansys, companies such as Siemens PLM, MSC Software, Abaqus also have presence in Pune.
Pune also has a growing list of companies that are using these engineering simulation softwares. Companies such as Cummins, John Deere, Dow Chemicals, Eaton Corp, Honeywell, etc have set up their product development centers in Pune which use these tools. Tata Motors, Tata Technologies, research wing of TCS, TRDDC and Tata’s new venture in HPC, CRL are also exploring the field of engineering simulations actively. Additionally engineering services consultants such as Tridiagonal, Pacific Mindware are also based in Pune.
Education institutes such as COEP too are now well equipped and have elective courses that allow students exposure to this interesting field.
About the author – Dr. Ajey Walavalkar
Ajey has over 10 years of experience in the Computational Fluid Dynamics industry. Currently, he is a Regional Support and Services Manager for Ansys Fluent India, in Pune. He has experience in successfully simulating various applications across industry domains, building teams of engineers for delivering CFD projects, support and services in an offshore setting. Ajey has a Ph.D. in Mechanical Engineering from Pennsylvania State University, USA, and a B.E. in Mechanical Engineering from COEP.